A Design for Remanufacture toolkit
Designing for a circular economy
Design for Remanufacture (D4R) is an area of product development that has grown in prominence with the increasing interest in how manufactured goods can be efficiently processed within a circular economy. The aim of this project was to create a D4R tool to facilitate the design for remanufacture process that was both easily understood and generally applicable across a range of industries.
The research team had a good understanding of current thinking on the topic, which highlighted that any design for remanufacturing tool needs to address all aspects of the remanufacturing process (e.g. from cleaning to testing). Initial feedback from industry contacts was that any tool would be more likely to be adopted and used if it could be applied with minimal or no training.
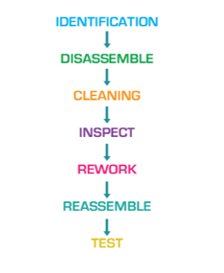
A generic seven step remanufacturing process was defined as the basis of the tool. Initial prototypes were reviewed by organisations involved in remanufacturing, and other academics working in the area; a diesel engine remanufacturer, Mackies, Isla Bikes, BeYonder, Egg Lighting, and Robert Gordon University. Following this, a workshop was held at the University of Strathclyde to map significant points at each stage of the remanufacturing process. Feedback from the workshop established that:
- There are few design features universally regarded as good or bad!
- Essentially what is regarded as desirable design features depends on the business model associated with the product.
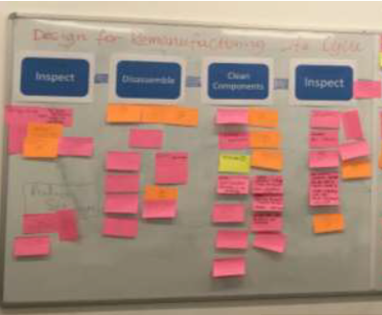
For example, quick release clips might be a desirable feature for a product designed to support 3rd world remanufacture, but a service model or an OEM owned remanufacturing service might what fastening that discouraged access.
As a result of this feedback the focus of the project changed from being a tool that provide a quantitative assessment to a tool that facilitated reflection and discussion of each step in the seven step process. A final prototype was developed which presented the user with a pack of double sided cards which illustrated different design features associated with each step in the process. Each step had a different colour to aid ease of use, and real life examples were included with each design feature.
To explain how the cards could be used a video was produced that illustrated to application of the cards to the design of a computer mouse.
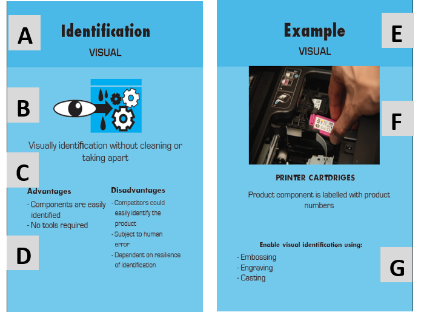
A. Name of a design solution to a Generic Process Step: In this case using visual identification.
B. Icon representing the design solution
C. One sentence description of the design solution
D. A list of advantages and disadvantage of adopting the design solution
E. On the reverse of the card is the title of an example
F. A photograph of the illustration
G. A list of ways the design solution could be implemented.
A Design for Remanufacture Toolkit
Accessing matched funding from the Scottish Institute for Remanufacture enabled the research team to produce and test a unique resource to support OEMs wishing to tailor new or existing products for remanufacturing processes. Over 200 packs of card have been printed and are currently being distributed at events (conferences, meetings and workshops) in Scotland and Europe. Further funding could be used to create a workshop for CPD courses and also develop and App based version. There has also been interest in producing sets of card tailored to the needs of specific industrial sectors (e.g. mountain bikes or buildings).
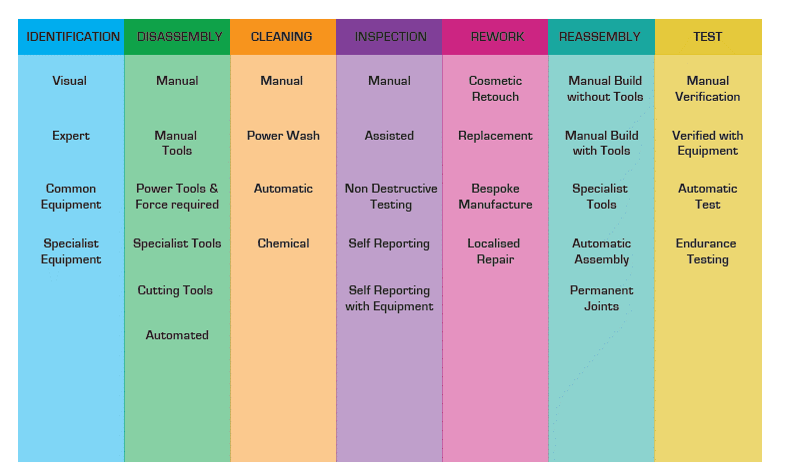