What is remanufacturing?
Remanufacturing is defined as the ‘process of returning a used product back to at least as-new condition with at least as – new guaranty.’ Dr Winifred Ijomah, Technical Director: Scottish Institute for Remanufacturing.
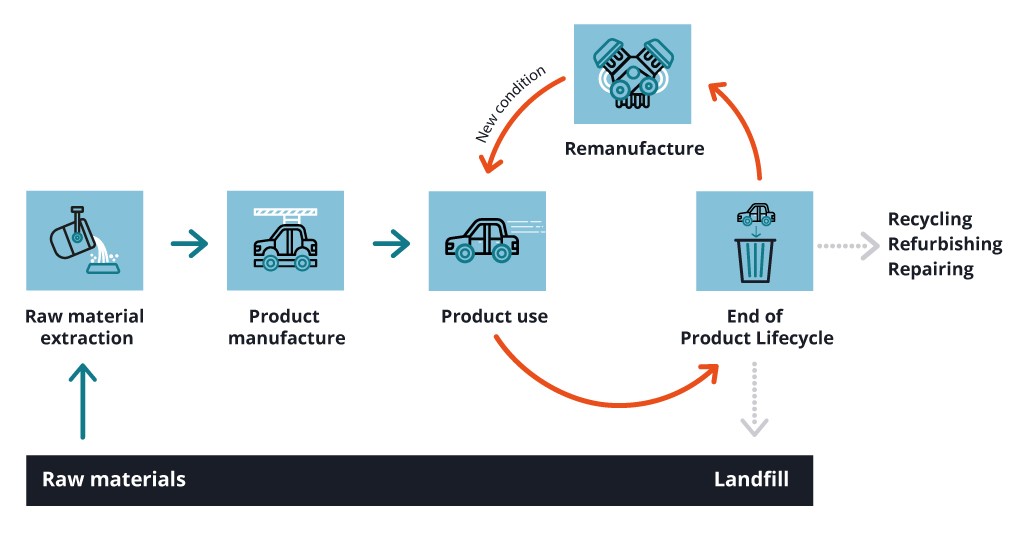
Including remanufacturing in our production process is essential. There are simply not enough materials available to sustain the traditional manufacturing method, which contributes to the 554 million tonnes of material consumed in the UK each year.
Remanufacturing a product begins a new lifecycle for that product. And when products are initially designed to be remanufactured, this process can continue indefinitely.
Remanufacturing cuts across many sectors in Scotland, with significant activity in aerospace, automotive and energy. In addition to this there are several sectors with strong growth potential for remanufacturing including ICT, medical equipment, furniture and rail.
What’s in a name?
Terminology used to describe remanufacturing can vary between sectors – titles such as servicing, overhauling, reconditioning and refurbishing are more familiar ways of talking about remanufacturing within some industries. When the process referred to fits the definition of remanufacturing, returning a used product back to at least as-new condition, then this is classed as remanufacturing.
However, remanufacturing is different, to other Circular Economy terms, namely re-use, repair and recycling and this difference needs to be noted.
Let’s look at an engine as an example:
The engine reaches the end of its lifecycle, either through the vehicle it was within no longer being of fit use, or the engine itself failing. There are a few choices as to what happens next:
Recycling: the engine is melted down and the resulting metals would be used elsewhere, across any number of products.
Repairing: if the engine had a fault a repair would fix the specific fault – without any guarantee as to how long that fix will work, or if there are any other wear and tear red flags in other parts.
Re–using: a functioning engine would see it taken as is, and put into another vehicle.
Remanufacturing: returning the engine as a whole, to as new, if not better, condition.
The video below features SIR Director, Dr Winifred Ijomah and showcases remanufacturing on a large scale at Herrenknecht in Germany, highlighting the benefits for both the Original Equipment Manufacturer (OEM) and the end customer.